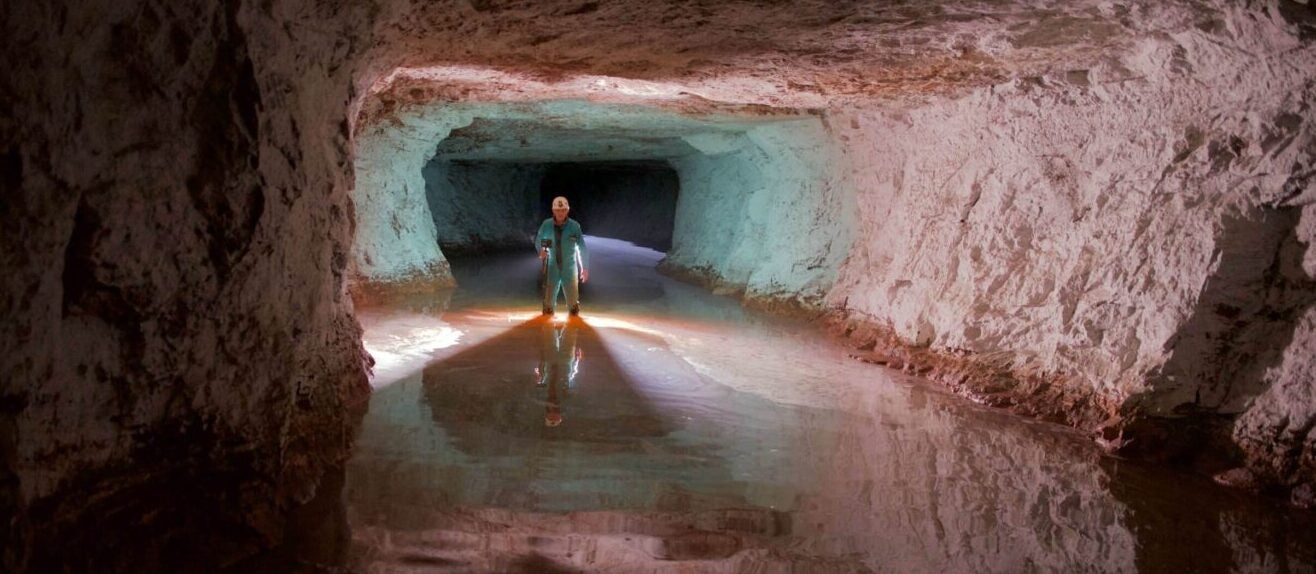
The presence of water in underground mines can halt operations, damage vehicles and equipment, and even risk contamination and becoming an environmental issue. Each mining site is different, so the nature and the extent of the flooding risk differs, but the demand for effective underground mine dewatering techniques is growing as mining operations are increasingly digging deeper.
Mine dewatering pumps
Submersible pumps or sump pumps for dewatering are essential tools for controlling water at mining sites and preventing flooding. Underground mine dewatering pumps are often submersible as they are better designed to handle debris without clogging, but there is a great deal of selection available for redirecting water underground.
The underground mine dewatering pump system that is chosen can depend on the specific layout of a mine, including the choice between using a single large pump to remove water or several smaller pumps in a multi-stage approach.
Mine dewatering pump selection
There are a lot of rugged, reliable underground mining dewatering pumps on the market, so mines will have no problem finding efficient equipment. The problem often lies with choosing the most suitable solution and weighing up the options between higher investment in larger pumps and the cost of excavation for space when using multiple smaller pumps.
This problem is solved by putting trust in mining safety experts who can find the best underground mine dewatering solution for a mine’s specific requirements. Along with an extensive stock of dewatering equipment, Carroll Technologies partners with Equipment Pro to custom-design pumping dewatering solutions for any situation. Equipment Pro’s pump vertical turbines and dewatering pumps can handle any type of pumping situation and have been by a range of industries across the US.
According to Carroll Technologies president, Allen Haywood: “Carroll provides Equipment Pro pump-turbine systems and different model pumps for different situations around mining facilities. We can arrange for there to be an automatic pumping solution so that there’s not a lot of maintenance required, and those pumps can turn on and turn off according to the volume of water that they need or that they want to keep a level down to.
“For any type of pumping requirements that a customer may have, large or small, a custom pumping solution can be designed. Large requirements may be a very complex situation with pumps, so we can build floating systems, pontoon systems, where these pumps are stationed.”
Additionally, Stancor Pumps has an extensive portfolio of MSHA-approved mine dewatering pumps designed to redirect water in confined spaces. The company’s portfolio includes the explosion-proof P/S Series of heavy-duty, dewatering pumps that offer excellent wear resistance, as well as the SL Solids Seriesvortex trash pumps, SEW solids handling wastewater pumps, and SB Series of clean water dewatering pumps.
Other mining equipment experts include Mefcor, which offers simple clog-resistant pumping solutions for difficult dewatering applications. Mefcor underground dewatering pumps do not require a power source or maintenance.